Wykorzystanie narzędzi lean manufacturing w logistyce firm produkcyjnych
Na czym polega Milkrun? Czym jest Kanban? Lean manufacturing oferuje szereg sprawdzonych rozwiązań logistycznych dla przemysłu. Pozwalają wyeliminować marnotrawstwo czasu i energii, wspierając produkcję
w przepływie.
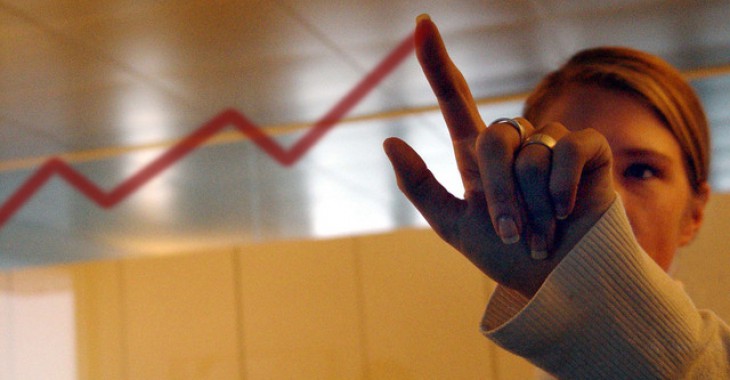
Nasze przyzwyczajenia mają znaczenie. Widać to także w logistyce firm produkcyjnych. Niektóre schematy porządkowania i dostarczania komponentów czy materiałów są kompletnie nieefektywne – kosztują niepotrzebnie dużo czasu i wysiłku.
– Wszystkie czynności, które przyczyniają się do wytworzenia wartości, czyli tego, za co skłonny jest zapłacić klient, są potrzebne. Pozostałe to marnotrawstwo i trzeba je wyeliminować. To jest istota lean management – wyjaśnia Katarzyna Szczupał-Vieweg, prezes Staufen Polska, firmy zajmującej się wdrażaniem lean management.
Logika naczyń połączonych
Proces produkcji można sobie wyobrazić jak system naczyń połączonych. To, jak funkcjonują gniazda, komórki czy linie produkcyjne zależy m.in. od organizacji przestrzeni produkcyjnej, standardów serwisu maszyn, przezbrojeń, procedur w administracji, jak również od sprawności logistyki wewnętrznej.
– Celem „szczupłego zarządzania” jest uzyskanie produkcji
w przepływie. To znaczy, że produkt powinien przejść przez linię tak szybko, jak to tylko możliwe, oczywiście przy zachowaniu jak najwyższej jakości – wyjaśnia Katarzyna Szczupał-Vieweg.
Jak uzyskać tego rodzaju przepływ? Najważniejsza jest synchronizacja poszczególnych elementów łańcucha wytwarzania, a logistyka odgrywa tu kluczową rolę – od dostaw zewnętrznych, przez strukturę magazynów, po sposób dostarczania poszczególnych komponentów, półproduktów czy materiałów na linię produkcyjną.
– Kluczem do usprawnienia przepływu jest likwidacja tzw. wąskich gardeł, czyli miejsc, w których marnuje się czas lub buduje niepotrzebne zapasy, spowalniając przejście produktu – dodaje Katarzyna Szczupał-Vieweg.
Lean management, filozofia zarządzania wypracowana na podstawie doświadczeń Toyoty, daje sporo rozwiązań tego rodzaju problemów, sprawdzonych w różnych branżach i w przedsiębiorstwach znajdujących się w różnej sytuacji.
Logistyka zewnętrzna
Problematyczne bywa zarządzanie dużymi zbiorami tanich komponentów. Jedna z firm miała około 2 tysiące drobnych referencji, m.in. śrubek, podkładek itp. Po pierwsze trudno w pełni kontrolować tego rodzaju zasoby, po drugie nakład potrzebnej do tego pracy jest nieadekwatny do wartości materiałów.
– Zdefiniowaliśmy grupy komponentów tak, by cały proces ich uzupełniania i dostarczania kontrolowali dostawcy. Coraz więcej firm w Polsce przechodzi na taki system, ponieważ pod każdym względem jest wygodniejszy, tańszy, a przede wszystkim bardziej efektywny – mówi Grzegorz Gawroński, senior consultat Staufen Polska.
Sposobem na usprawnienie rotacji w logistyce zewnętrznej jest tzw. Milkrun. To metoda łączenia różnych transportów (między dostawcami a firmą) tak, żeby samochody dostawcze jeździły zawsze optymalnie załadowane, czyli nie tylko z pełnym wykorzystaniem przestrzeni ładunkowej, lecz również wyłącznie z takimi materiałami, które są potrzebne. Dlatego cykle trzeba dostosować do zapotrzebowania na określone komponenty czy podzespoły w procesie produkcji.
Magazyn uporządkowany
Pracownicy poruszają się tylko w jednej alejce, dzięki czemu bardzo dobrze znają swój rejon magazynu. Komponenty używane częściej leżą niżej, a przez to są łatwiej i szybciej dostępne. Są także uporządkowane analogicznie do struktury gniazd produkcyjnych. Poszczególne komponenty, półprodukty czy podzespoły trafiają na kolejne etapy produkcji według zasady Just-in-Time – dokładnie
w tym momencie, kiedy są potrzebne.
– Tak uporządkowany magazyn generuje mniej ruchu, co przekłada się na oszczędności na czasie i transporcie, ale także wzrost poziomu bezpieczeństwa. Poza tym znacznie redukuje się w ten sposób zapasy. Docelowo pozwala to ograniczyć powierzchnię magazynową – opowiada Grzegorz Gawroński.
Dostarcz, gdy potrzeba
Jednym z typowych sposobów usprawniania rotacji materiałów w ramach lean management jest metoda Kanban. Słowo pochodzi z języka japońskiego i oznacza „kartę” lub „tablicę”, ale lepiej to tłumaczyć jako „widoczny znak”. Idea jest prosta – proces dostarczania materiałów do gniazd czy komórek produkcyjnych
w przejrzysty sposób zorientować na rzeczywiste zużycie tych elementów. Metoda Kanban polega na wywoływaniu działania (dostawy) w momencie, gdy określone komponenty są potrzebne.
Jak takie zmiany wyglądają w praktyce? W polskiej firmie produkującej nadwozia samochodowe do wytworzenia jednego produktu potrzeba 600 komponentów. Logistyka wewnętrzna działała tam skrajnie nieefektywnie, ponieważ do każdego zlecenia wszystkie komponenty były pakowane osobno. Wymagało to bardzo dużo czasu i angażowało wielu ludzi.
– Jednak około 40% to były komponenty standardowe, które można było dostarczać w systemie kanban. Poza tym zreorganizowaliśmy magazyn pod kątem przepływu strumienia wartości, co bardzo skróciło czas zbierania komponentów. W sumie uzyskaliśmy w ten sposób wzrost wydajności dostaw o około 20% - mówi Grzegorz Gawroński.
W polskiej firmie produkującej ramy do siedzeń samochodowych system dostaw, zarówno wewnętrznych, jak i zewnętrznych, został zorganizowany tak sprawnie, że zakład ma zapasy tylko na 12 godzin. – Jeśli dokładnie zaplanujemy, ile materiału potrzeba, zlikwidujemy wąskie gardła i w pełni zsynchronizujemy logistykę z całym łańcuchem wytwarzania, to proces będzie przebiegał optymalnie, czyli bez marnotrawstwa – dodaje Grzegorz Gawroński.
Źródło: Staufen
Fot. www.freeimages.com