Niezbędny choć ryzykowny
Działania personelu produkcyjnego mają ogromny wpływ na jakość leku. Z jednej strony pracownicy mogą wykryć i zniwelować powstałe odchylenie, a z drugiej mogą go w ogóle nie zauważyć lub wręcz zataić. Jak uniknąć niebezpiecznych sytuacji spowodowanych nieprawidłowym zachowaniem kadry? Należy szkolić, szkolić i jeszcze raz szkolić.
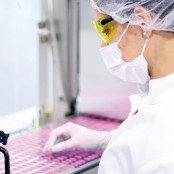
Cały proces wytwarzania leku musi przebiegać według ściśle określonej procedury – tylko wtedy powstaje produkt zgodny ze specyfikacją. W praktyce zdarzają się jednak odchylenia. Mogą one dotyczyć różnych etapów wytwarzania, tj. przygotowania roztworu, napełniania czy pakowania. Liczba i możliwość wystąpienia odchyleń są trudne do określenia, ale tylko pełna informacja na temat przebiegu procesu produkcyjnego i umiejętność oceny zagrożeń wynikających z odchyleń pozwalają stwierdzić, czy możliwe jest otrzymanie bezpiecznego produktu farmaceutycznego. Metody badań, którymi się w tym celu posługujemy, mają często charakter niszczący, dlatego zmuszeni jesteśmy do pobierania prób i zachowania reguł statystyki. Jest to jednak postępowanie uzasadnione tylko w przypadku serii jednorodnych. Problem pojawia się, gdy nie wiemy o czymś, o czym powinniśmy wiedzieć. Jeśli zdarzenie dotyczy urządzeń, istnieje szansa, że zostaniemy o nim poinformowani poprzez automatyczne włączenie się alarmu ostrzegawczego. Zupełnie inaczej wygląda sytuacja, gdy niezgodność może być dostrzeżona wyłącznie przez pracownika, który powinien ją zgłosić lub zapisać.
Tragiczny wypadek
Jednym z tragiczniejszych przypadków obrazujących ten problem była sytuacja w 2000 roku w zakładzie produkcyjnym firmy Schering Plough, gdzie w trakcie napełniania nebulizatorów odłączył się przewód doprowadzający substancję czynną do urządzenia napełniającego. Niestety urządzenie nie zgłosiło awarii w sposób pozwalający wyeliminować puste opakowania, zaś mechanik podłączył przewód ponownie i produkcja była kontynuowana. Osoby odpowiedzialne za zwolnienie leku nie były poinformowane o tym zdarzeniu, a kontrola jakości nie trafiła podczas rutynowych badań na wadliwe opakowanie, więc produkt został zwolniony do obrotu. Wśród pacjentów, którzy nabyli wadliwy lek, zgłoszono 17 wypadków śmiertelnych, a firma poniosła znaczące koszty związane z wycofaniem produktu z rynku oraz nałożonymi na nią karami.1 Brak informacji stał się więc przyczyną tragedii. Gdyby mechanik zgłosił odpowiednim osobom awarię, zostałyby wdrożone określone działania, które pozwoliłyby uniknąć nieszczęścia.
Kontrola stuprocentowa?
Nie można liczyć, że wszelkie tego typu zdarzenia będą wychwycone przez systemy kontroli jakości – w zakładzie produkcyjnym, nawet jeśli istniałyby techniczne i technologiczne możliwości sprawdzania wszystkich parametrów we wszystkich opakowaniach jednostkowych, to w praktyce oznaczałoby to taki wzrost kosztów, że produkcja byłaby nieopłacalna. Dlatego też metody kontroli są dopasowane do możliwości nie tylko technologicznych, ale też finansowych producenta. Podejmowane są działania mające na celu wprowadzić taki nadzór nad procesem, by zapobiegać powstawaniu błędom, i ograniczyć koszty z nich wynikające. Tego typu działania stają się bardziej intensywne po tragediach spowodowanych niepożądanymi działaniami produktów leczniczych. Procedury mające za zadanie zapobiegać błędom tworzą system zapewnienia jakości. Dla przemysłu farmaceutycznego jest on oparty na przepisach GMP, opisanych w załączniku do Rozporządzenia Ministra Zdrowia z dnia 1 października 2008 roku z późniejszymi zmianami. Każdy producent europejski musi przestrzegać tych zasad – przechodzi okresowe inspekcje przeprowadzane przez upoważnione władze, prowadzi wymagane walidacje i kwalifikacje.
Personel a jakość produktu
Na proces wytwarzania duży wpływ ma personel produkcyjny zakładu farmaceutycznego – zaczynając od sprzątaczek, przez operatorów i mechaników, aż po mistrzów i kierowników. Oddziaływanie tych osób na jakość produktu można podzielić na bezpośrednie i pośrednie (rys. 1).
Wpływ bezpośredni
Najbardziej oczywiste wydaje się oddziaływanie bezpośrednie. Wynika ono z naturalnej fizjologii organizmu, związane jest z nieznajomością obowiązujących procedur lub też spowodowane brakiem świadomości co do konsekwencji nieprzestrzegania procedur lub zachowań odruchowych.
Fizjologia organizmu
Nawet stojący bez ruchu człowiek uwalnia 100 tys. cząsteczek powyżej 0,3 μm/min. Są to fragmenty naskórka, rzęsy, włosy. Mogą to być fragmenty makijażu – cząstki pudru, cieni do powiek, tuszu do rzęs. Jak duże znaczenie mają takie drobiny w produkcji leków – to zależy: od wymagań czystości mikrobiologicznej stawianych produktom leczniczym w określonej postaci. Przy produkcji form doustnych jest to istotne, przy produktach sterylnych krytyczne. Dlatego te drugie muszą być wytwarzane w odpowiednich klasach czystości opisanych w aneksie I wymagań GMP. W klasie czystości A mówimy o konkretnych ilościach cząstek powyżej 0,5 μm i powyżej 5 μm w powietrzu. Posługujemy się nawiewami laminarnymi o określonej prędkości przepływu powietrza (0,45 ± 0,09 m/s), filtrami HEPA (H13-H14 – zatrzymującymi 99,95% cząstek o wielkości powyżej 0,3 μm) i zwracamy szczególną uwagę na wszelkie działania, które mogą wprowadzić dodatkowe – niekontrolowane cząstki do środowiska pracy lub choćby zaburzyć wymuszoną przez nas cyrkulację powietrza.
Prócz zanieczyszczeń fizycznych wyróżnia się te mikrobiologiczne – a więc naturalną florę bakteryjną obecną na skórze i śluzówkach zdrowego człowieka. Nie ma możliwości eradykacji tych mikroorganizmów, gdyż tworzą one naturalną barierę organizmu, jednak w przypadku nieprzestrzegania higieny, mogą zakazić produkt leczniczy.
Można przyjąć, że „fizjologiczny” wpływ pracownika na jakość produkowanego leku jest w pełni znany, dzięki czemu mamy możliwości znalezienia i zastosowania odpowiednich rozwiązań dostosowanych do wymogów danej produkcji, tak aby w maksymalnym stopniu wyeliminować zagrożenie.
![]() |
Odchylenia w procesie produkcji
Ten rodzaj wpływu dzieli się na dwie główne kategorie: wynikający ze świadomego działania oraz wynikający z braku wiedzy. U podłoża obu grup problemów leży brak szkoleń – takich, które zbudują odpowiednią świadomość u pracownika oraz zmotywują go do działania w przypadku odchyleń w procesie produkcji.
Nieświadomy wpływ personelu
Wydaje się, że jest to najczęstsza interakcja pracownika, mogąca mieć wpływ na jakość leku. Chodzi tu głównie o jego zachowanie, które wynikać może ze zmęczenia, niewiedzy lub lenistwa, a które może mieć znaczący wpływ na jakość produktu. Należy tu wymienić na pierwszym miejscu higienę, rozumianą jako całokształt zasad, których celem jest zachowanie odpowiedniej czystości oraz zdrowia. Ważne jest też odpowiednie zachowanie i nie chodzi bynajmniej o bycie uprzejmym.
![]() |
Może się zdarzyć, że pracownikowi na podłogę spadnie długopis, a ten odruchowo go podniesie. Niby nic, jednak jego ręka, a w przypadku gdy ma rękawice ochronne – właśnie one – zetkną się z podłożem. Może być tak, że kichnie i przetrze nos rękawem. Jest tu wiele różnych możliwości, które sprowadzają się do jednego – zachowa się „normalnie”, nie zwracając uwagi na fakt, że nie jest w „normalnej sytuacji”, ale w miejscu pracy. O ile w przypadku procesu pakowania w kartoniki zamkniętych blistrów czy nawet ampułek, takie zachowanie można określić jako niewskazane, ale jednak niepowodujące ryzyka, które mogłoby zagrozić życiu pacjenta, o tyle w przypadku wykonywania czynności przy otwartym produkcie, są to zdarzenia niedopuszczalne.
Szczególną sytuacją jest wytwarzanie produktów sterylnych niesterylizowanych termicznie w opakowaniu końcowym. Tego rodzaju produkcja odbywa się w pomieszczeniach o najwyższych klasach czystości, w których konieczne jest przestrzeganie specyficznych i bardzo restrykcyjnych zasad zachowania się. Należy ograniczyć ruchy do niezbędnego minimum, wykonywać je powoli, nie wchodzić bezpośrednio w obszar napełniania, nie powinno się rozmawiać. Zasady te mają zapewnić, że warunki wytwarzania będą prawidłowe, a człowiek swoją obecnością nie spowoduje wzrostu ilości cząstek powyżej określonych limitów i nie stanie się źródłem wtórnego zakażenia mikrobiologicznego produktu. W trakcie inspekcji w zakładach wytwarzających produkty sterylne inspektorzy zwracają na to szczególną uwagę. Dowodem na to może być Warning Letter opublikowany przez FDA w dniu 14 lipca 2011r., w którym znajduje się stwierdzenie – „personel w kabinie nie poruszał się wolno i w sposób celowy”.
Ponieważ nie ma możliwości, aby osoba nadzorująca znajdowała się przy pracowniku przez 8 godzin, pracownik wykonujący monotonną pracę często nie kontroluje pewnych odruchów czy zachowań – nie będąc świadomy konsekwencji takiego postępowania nie będzie ich unikał. Dlatego też prowadzone są odpowiednie szkolenia, w trakcie których przedstawia się, jakie są wymagania w tym zakresie, jak również uświadamia się pracownikom, czym podyktowana jest dana zasada i że nie stanowi ona widzimisię przełożonego.
W aspekcie mikrobiologii, nieświadome działania to brak wiedzy o stanie swojego zdrowia – choroby, takie jak choćby schorzenia skóry czy próchnica, których dana osoba może na pewnym etapie nie zauważyć, mają znaczący wpływ na ilość i rodzaj generowanych zanieczyszczeń mikrobiologicznych. Czasem taki wpływ ma nienaturalna flora bakteryjna skóry – co może mieć miejsce w przypadku osób mających zwierzęta domowe. Kluczem jest tu przestrzeganie zasad higieny osobistej i to nie tylko na terenie zakładu produkcyjnego, ale również w życiu codziennym. Elementem wspomagającym jest konieczność przechodzenia okresowych badań lekarskich, które obejmują m.in. kontrolne wizyty u stomatologa i dermatologa. Częstotliwość i zakres badań uzależniony jest od rodzaju pracy wykonywanej przez daną osobę.
Szczególny przypadek stanowią pracownicy prowadzący ręczny przegląd optyczny na zanieczyszczenia mechaniczne obecne w ampułkach lub fiolkach produktów przeznaczonych do wstrzykiwań. Ten etap wytwarzania jest krytyczny dla bezpieczeństwa pacjenta. Pracownicy oczywiście muszą odbyć specjalistyczne szkolenia, ale również muszą co pół roku przechodzić badania okulistyczne. Ma to zapobiec sytuacji, w której nastąpi pogorszenie wzroku utrudniające lub wręcz uniemożliwiające pracę przy przeglądzie, a którego sam pracownik nie będzie w stanie zauważyć.
Rys. 1. Sposoby oddziaływania personelu na jakość produktu leczniczego
Świadomy wpływ personelu
Tutaj ilość możliwych do zaistnienia sytuacji jest ogromna: od z pozoru błahych działań, takich jak pośpiech przy zakładaniu ubrania ochronnego i wynikająca z niego niechlujność, aż po niezgłoszenie odchylenia, o którym pracownik wie, że może mieć wpływ na jakość gotowego produktu.
Niestety, gdy mówimy o świadomym działaniu personelu, które może mieć wpływ na obniżenie jakości produktu końcowego, mamy wyłącznie dwa sposoby oddziaływania: budowanie świadomości pracowników odnośnie ich działania i konsekwencji oraz nadzór nad ich pracą. Pierwsze oddziaływanie jest czasochłonne i długotrwałe – proces szkolenia pracownika np. zatrudnionego przy produkcji form iniekcyjnych, to wiele tygodni nauki i wiele miesięcy pracy, zaś dla jego przełożonych – wiele godzin szkoleń i nadzoru merytorycznego. Drugi sposób działania, a więc nadzór nad ich pracą – jest trudny do realizacji – nie ma tak dużej ilości kadr, aby móc go sprawować non-stop. Dlatego wszystko musi opierać się na kontrolowanym zaufaniu, cierpliwości i szkoleniach.
![]() |
Nie bez znaczenia pozostają też predyspozycje poszczególnych osób do zajmowania danych stanowisk. Ktoś, kto jest osobą „szybką i energiczną”, może mieć trudności z odnalezieniem się w pracy jako operator maszyny w strefie czystej w produkcji leków iniekcyjnych, gdzie musi poruszać się wolno, niezależnie od sytuacji, zaś z drugiej strony będzie się doskonale sprawdzał jako operator urządzeń pracujących w innych strefach, gdzie szybkość poruszania się nie ma tak dużego znaczenia.
![]() |
Wpływ pośredni
Największy problem, jaki może się pojawić w przypadku pośredniego oddziaływania personelu na jakość produktu leczniczego, to trudności komunikacyjne. Może to być konsekwencją źle zaplanowanego obiegu dokumentacji, braku czasu, braku zaufania czy choćby atmosferą na wydziale produkcyjnym. Każdy z tych czynników jest inny i każdy wymaga odrębnych działań, jednak wszystkie sprowadzają się do jednego – pracownik nie informuje o odchyleniu, które może mieć wpływ na jakość produktu – najczęściej, aby uniknąć konsekwencji z tym związanych. Niestety, w ten sposób może narażać życie innych osób – pacjentów – lub narażać wytwórcę na dużo większe straty finansowe.
Źle zorganizowany obieg dokumentacji
Każda dokumentacja powinna być zaplanowana lub korygowana przez osoby mające doświadczenie w produkcji. Dzięki takiemu podejściu jest ona bardziej elastyczna i dostosowana w większym stopniu do realiów panujących na wydziale. Nie można tu dopuścić do sytuacji, gdy o jakimś zdarzeniu nikt nie jest informowany, ponieważ „nie było gdzie tego wpisać” lub „nikt tego nie wymaga, skoro nie ma tego w tabelce”.
Nieodpowiednie planowanie
Wytworzenie produktu leczniczego jest procesem przebiegającym w określonym czasie. Planując produkcję konieczne jest uwzględnienie tego czasu, ale również czasów niezbędnych do przygotowania i wyczyszczenia urządzeń. Zaplanowanie większej ilości serii niż wynika to z rzeczywistych czasów może doprowadzić do chwilowego wzrostu efektywności. Jest wtedy jednak duże prawdopodobieństwo, że ludzie zastosują skróty – krócej będzie trwał proces mieszania albo suszenia, a może sprzątanie będzie mniej dokładne, bo to najtrudniej zweryfikować. W konsekwencji być może otrzymamy większą ilość produktu, ale nie będziemy mieli pewności, że spełni on wymagania specyfikacji. Podobne konsekwencje może mieć ograniczenie zatrudnienia. Konieczność pracowania „za dwóch” prowadzi do napiętej atmosfery, przemęczenia ludzi, a wtedy łatwiej zapomnieć o konieczności wypełnienia wszystkich niezbędnych formularzy, szybciej popełnia się błędy.
Atmosfera w miejscu pracy
Jest to jeden z częstszych problemów. Nikt nie idzie do pracy, aby martwić się sytuacją innych osób lub aby rozwiązywać ich problemy. Nie zwalnia nas to jednak z obowiązku poszanowania innych osób i dbania o poprawne stosunki między pracownikami.
Wystarczy, że pracownik będzie miał świadomość, że jeśli zgłosi błąd, to będzie to równoznaczne z jego winą, aby unikać zgłaszania odchyleń i udawaniu, że o niczym nie wie. W sytuacji, kiedy pracownik przychodzi i informuje o swoim błędzie, bardzo ważna jest reakcja i postępowanie przełożonych. Muszą być oni przygotowani na wysłuchanie pracownika. Przed ukaraniem go powinni rozważyć, czy nie lepiej zamiast kary poszukać rozwiązań, które ułatwią lub zapobiegną w przyszłości podobnym błędom.
Brak umiejętności oceny odchylenia
Problem ten może mieć kilka wymiarów – pierwszy, dosłowny, to inaczej brak odpowiedniej wiedzy merytorycznej popartej doświadczeniem, przez co odchylenie, które dyskwalifikuje produkt, będzie potraktowane jako odchylenie nieistotne, a lek zostanie zwolniony do obrotu. Rozwiązaniem jest tu sprawdzanie i ocena odchylenia przez kilka osób o różnych kwalifikacjach, np. odchylenie zgłasza osoba, która je zaobserwowała, a oceny odchylenia dokonuje kierownik wydziału/oddziału, następnie jest ono weryfikowane przez wyznaczoną osob ę w dziale Zapewnienia Jakości oraz przez Osobę Wykwalifikowaną. Dzięki temu każde odchylenie jest oceniane przez kilka osób o różnym spojrzeniu.
Drugi wymiar tego problemu to zgłoszenie odchylenia przez pracownika mistrzowi, który musi natychmiast podjąć decyzję co do toku postępowania – czy sytuacja jest na tyle krytyczna, by wstrzymać produkcję i przekazać informację dalej, w celu rozwiązania problemu i bardziej kompleksowej oceny odchylenia przez kierownika produkcji i/lub Osobę Wykwalifikowaną, czy jednak jest na tyle drobna, że można kontynuować proces wytwarzania szkoleń?
Odpowiednio przygotowane szkolenie nie tylko wskazuje na sposób zachowania w danej sytuacji lub kładzie nacisk na znajomość procedury, ale przede wszystkim tłumaczy, dlaczego pewne działania są niezbędne i jaka jest przyczyna takiego zachowania. W efekcie dobrze przeszkolony pracownik nie tylko prawidłowo się zachowuje przez większość swojego czasu pracy, ale przede wszystkim w sytuacji nietypowej umie podjąć samodzielnie odpowiednią decyzję.
Szkoląc pracowników nie można zapominać o osobach szkolących. Kurs osób dorosłych ma swoje prawa – są to bowiem ludzie mający swoje doświadczenie i wiedzę, wrażliwi na krytykę i podważanie ich kompetencji. Prowadząc dla nich szkolenie trzeba przystosować sposób prezentacji i przekazywania informacji do ich oczekiwań i możliwości. Należy pozwolić na samodzielne wyciąganie wniosków i bazować na ich doświadczeniu, choć z drugiej strony trzeba sprawdzić, czy wnioski te są poprawne i zgodne z intencją osoby szkolącej. Dlatego osoby prowadzące szkolenia powinny być odpowiednio przygotowane.
Ktoś mógłby powiedzieć, że jako manadżer lub mistrz nie jest po to, aby szkolić personel produkcyjny, a jego celem jest produkcja na odpowiednim poziomie. Nie można się z tym zgodzić. Duże zaangażowanie w szkolenie i budowanie świadomości pracowników pozwala na zaoszczędzenie wielu kosztów w późniejszych działaniach. Pojawia się tu pytanie – czy lepiej jest cierpliwie tłumaczyć i przekazywać wiedzę, a w konsekwencji mieć dobrze przygotowaną załogę i niski współczynnik odchyleń, czy wymagać od innych wielu ważnych rzeczy, o których nie mają pojęcia, a w konsekwencji borykać się z problemami jakościowymi? Tak jest często w przypadku pracowników zatrudnianych okresowo przez pośredników lub przy dużej rotacji zatrudnienia, gdy pracownik nie ma czasu na odpowiednie przeszkolenie i zdobycie doświadczenia, zaś w zakładzie nie ma osób, które mogłyby wiedzę przekazać.
Szkolenia mają wymierny wpływ na finanse zakładu, ale nie można tego rozpatrywać jako wydatków. Są to oczywiście koszty, ale przynoszące wymierne korzyści finansowe lub, jak kto woli, pozwalające uniknąć zdecydowanie wyższych i nieprzewidywalnych kosztów. Jeśli zestawimy koszty szkoleń z kosztem zniszczenia serii, które mogą się wahać od kilku tysięcy złotych do kilkudziesięciu, a nawet więcej, to nakłady na szkolenia są relatywnie niskie. Nie wspominając już o problemach z wizerunkiem marki danego produktu lub wręcz producenta, jeśli w grę wchodzi wycofanie leku z rynku.
* * *
Człowiek to najbardziej ryzykowny i zawodny „element” procesu wytwarzania. Mimo licznych prób wyeliminowania obecności ludzi podczas procesu produkcyjnego, nie daje się tego osiągnąć w 100%. Człowiek zawsze pozostaje na końcu każdego etapu, bo nawet jeśli nie będzie bezpośrednim wykonawcą, to do niego należy ostateczna ocena zaistniałych zdarzeń. Człowiek musi zweryfikować zarejestrowane parametry, a także określić, czy proces był prawidłowy, czy zarejestrowane odchylenia wpłynęły na jakość produktu.
Jedynym rozwiązaniem, pozwalającym na zmniejszenie ryzyka związanego z obecnością człowieka w procesie produkcji, jak i pojawiającymi się problemami technicznymi, jest systematyczne szkolenie, które nie tylko uczy zachowania w danej sytuacji, ale buduje świadomość i przygotowuje do funkcjonowania w sytuacji, której nikt nie przewidział. Opieranie się na podejściu, że pracownik może się nauczyć pracować od miejsca A do miejsca B i nic więcej nie musi wiedzieć, jest błędne, o czym świadczy przykład z firmy Shering Plough przedstawiony na początku artykułu – bo przecież, gdyby ktoś przewidział, czym groziła ta sytuacja, na pewno wdrożyłby działania pozwalające na jej uniknięcie. A pracownik umiejący myśleć i działać nie miałby problemu z tą sytuacją i żadne koszty szkoleń nie byłyby za wysokie, gdyby pozwoliły ocalić choćby jedno ludzkie życie.
Literatura:
[1] Andrzej Szarmański, „Sztuka zarządzania jakością”, „Przemysł Farmaceutyczny” nr 1/2011.
Autor: Ewa Prymek, Polfa Warszawa S.A.
Artykuł został opublikowany w magazynie "Przemysł Farmaceutyczny" nr 4/2012
Źródło fot.: photogenica.pl