Walczymy z firefightingiem
– Rozwiązujemy problemy, ale nie na zasadzie gaszenia pożaru. Im mniej firefightingu, tym lepiej. Oczywiście, jak w każdej fabryce, awarie się zdarzają, są to jednak sporadyczne przypadki. Z ideologicznego punktu widzenia dążymy do stanu: „zero awarii” – mówi Przemysław Soloch, menedżer ds. technicznych w poznańskiej fabryce GSK.
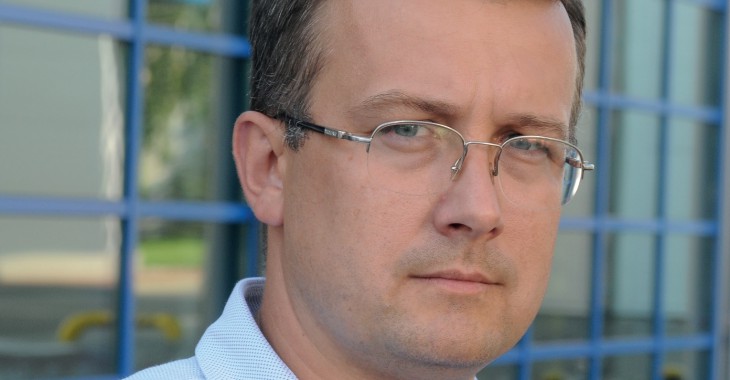
- Jak długo „żyją” maszyny w waszej fabryce?
To zależy, co dane urządzenie robi, ale zwykle jest to od 10 do 15 lat. Na jednym biegunie są maszyny mało eksploatowane, proste w konstrukcji oraz te związane z infrastrukturą techniczną. Na drugim – urządzenia laboratoryjne, które nie są w stanie „przeżyć” w dobrej kondycji nawet 10 lat, gdyż wykonują ogromną liczbę cykli roboczych w krótkim okresie. Poza tym czasem ich wymiana jest konieczna po prostu ze względu na zmieniające się wymagania.
- Czy na podstawie doświadczeń GSK może pan powiedzieć, że „mercedes” gwarantuje redukcję awaryjności?
Nie ma jednoznacznej odpowiedzi. To indywidualna kwestia każdego przypadku. Na pewno nie zawsze opłaca się kupować najtańsze urządzenie. Musimy mieć świadomość, że koszty zakupu maszyny wracają w kosztach operacyjnych i w amortyzacji. Koszty inwestycji powinny więc być optymalne – ani nie za niskie, ani nie za wysokie. Za niskie powodują, że awaryjność będzie wysoka, lub cykl życia zbyt krótki, a to wpływa na cenę wyrobu gotowego. My staramy się kupować urządzenia, które są przede wszystkim trwałe. Zwracamy uwagę na ich rozwiązania techniczne i konstrukcję.
- W tej chwili wymaga się od urządzeń coraz wyższych efektywności.
Zgadza się. Dotyczy to przede wszystkim maszyn stricte produkcyjnych. Tutaj ważne są szybkość i łatwość przezbrojeń, żeby jak najwięcej czasu wykorzystać na faktyczną pracę. Czym większa dostępność urządzenia, tym może ono z siebie więcej dać.
- A czy zwracacie uwagę na serwis posprzedażowy?
To jest standard. Nie możemy jednak zakładać serwisu posprzedażowego jako czegoś, co realizuje nam w fabryce wszystkie zadania maintenance’owe. Po to mamy swoje służby techniczne, żeby były przeszkolone do samodzielnego przeprowadzenia diagnostyki i wykonania serwisu. Musimy mieć możliwość szybkiej reakcji, dostęp do części zamiennych oraz dodatkowe wsparcie techniczne. Całość bieżącej obsługi jest więc w naszych rękach. Dlatego też kładziemy nacisk na szkolenia naszych pracowników – są one jedną z części inwestycji przy zakupie nowej maszyny.
- Jakie są proporcje między pracą waszych mechaników a tych z firmy zewnętrznej?
Jeżeli mówimy o rozruchu urządzenia to pełną odpowiedzialność bierze dostawca. Duże przeglądy okresowe w zależności od typu maszyny mogą być realizowane przez firmę zewnętrzną, ale nie zawsze mamy takie wymagania. Core biznes, czyli utrzymanie ruchu maszyn produkcyjnych, staramy się prowadzić sami. Dużo więcej outsourcujemy w przypadku obiektów infrastruktury. Patrząc na proporcje ilościowo, jest to ok. 50/50. Ważniejszy jest jednak podział merytoryczny – element kontrolny leży po stronie pracowników GSK, zaś element wykonawczy po stronie firmy zewnętrznej. Mamy kilka firm serwisujących, z którymi współpracujemy praktycznie na stałe.
- Czy zdarzyło się kiedyś, że modyfikacja autorstwa waszych ludzi została wdrożona przez producenta maszyny do nowego modelu?
Staramy się, żeby dostawca był cały czas odpowiedzialny za urządzenie. Podczas modernizacji czy zakupu nowej maszyny zgłaszamy to, co należałoby poprawić, dajemy nasze sugestie. Oczywiście są to drobne zmiany, które mają usprawnić ergonomię czy wpłynąć na łatwość obsługi z punktu widzenia operatora albo technika. Drobne rzeczy modernizujemy samodzielnie – mamy całą grupę automatyków w GSK. Są to jednak rzeczy, które nie wpływają na konstrukcję całego obiektu.
- Lepiej modernizować czy jednak kupić nowe?
Urządzenia farmaceutyczne są bardzo drogie. Raz zakupiona maszyna, żeby się spłacić, powinna pracować przez co najmniej 12-15 lat. Niektóre jej elementy muszą być unowocześniane po prostu w związku z postępem technologicznym. Chodzi tu przede wszystkim o systemy sterowania, które starzeją się kilka razy szybciej niż elementy mechaniczne. Warto jest więc w tym zakresie modernizować, a nie od razu kupować nowe.
- Czy zgodzi się pan ze stwierdzeniem, że służby UR to „rozwiązywacze problemów”?
Naszą rolą jest rozwiązywanie problemów. Staramy się jednak być o krok do przodu i identyfikować je już na etapie pierwszych niepokojących objawów. Pracujemy zgodnie z metodologią 4 M, która mówi o tym, że każdy proces czy każde działanie w produkcji składa się z: Man, Machine, Material, Management Method (Człowiek, Maszyna, Materiał, Metoda Zarządzania). Jeśli pojawiają się problemy, to znaczy, że mamy do czynienia z brakiem standardu w którymś z tych 4 M. Jeżeli maszyna pracuje poprawnie, to popatrzymy na materiał. Jeśli materiał jest OK, to sprawdzamy pracę
człowieka. Jeśli człowiek wykonuje działanie poprawnie, to błąd tkwi gdzieś w sposobie zarządzania.
Obszar techniczny ściśle współpracuje z technologią i z produkcją. Kiedy mamy problem, siadamy razem i wspólnie staramy się go rozwiązać. Chcemy coraz lepiej rozumieć proces, żeby dobrze identyfikować zmienne na niego wpływające.
- Czyli rozbieracie proces na czynniki pierwsze?
Na płynność podawania opakowania w kartoniarce wpływ może mieć drobne zagięcie kartonika, poślizg na ssawkach, zmienność w połysku materiału, dodatkowa chropowatość... Staramy się poznać wszystkie te szczegóły. Problemem może być zmienność, której my nie identyfikujemy. W tym przypadku skupia się nad tym operator, technik, technolog pakowania.
- Takie działanie można nazwać profilaktyką UR.
Rozwiązujemy problemy, ale nie na zasadzie gaszenia pożaru. Im mniej firefightingu, tym lepiej. Oczywiście, jak w każdej fabryce, awarie się zdarzają. Są to jednak sporadyczne przypadki. Z ideologicznego punktu widzenia dążymy do stanu: „zero awarii”. Niektóre urządzenia nie są krytyczne z punktu widzenia procesowego, dlatego mogą pracować do awarii, np. spłuczka w toalecie. Pompę natomiast planujemy już konserwować raz na rok czy raz na 2 lata w zależności od jej znaczenia. Nie czekamy aż się zepsuje i zacznie cieknąć.
- Ostatnio modne jest czerpanie inspiracji z innych branży. UR w farmacji wzoruje się m.in. na automotive. Dojście do takiego poziomu jest jednak w przemyśle farmaceutycznym raczej niemożliwe.
Ze względu na liczne regulacje z GMP na czele, farmacja jest trochę inna. Każda zmiana w tym przemyśle powoduje bowiem bardzo duży wysiłek dokumentacyjny, wdrożeniowy, kwalifikacyjny. Aby wprowadzić jedną zmianę, czasem potrzebne są lata. W automotive, w przemyśle spożywczym czy w przemyśle FMCG, jeśli mówimy o urządzeniach procesowych, dynamika zmian może być znacznie większa. GSK jako całość stara się patrzeć na inne przykłady.
Byliśmy na kilku wizytach referencyjnych u różnych producentów: i w Polsce, i za granicą, zapraszaliśmy również do Poznania. Staramy się wymieniać wiedzą. Przemysł spożywczy ma bardzo ciekawe rozwiązania, szczególnie jeśli chodzi o niezawodność. Skala produkcji (ilości ton) jest tam dużo większa od skali produkcji w farmacji, nawet jeśli procesy są podobne. Krótkie zatrzymanie urządzenia ma znacznie większy wpływ na wydajność pracy danego urządzenia.
Korzystamy również z doświadczenia, jakim była wizyta w fabryce wytwarzającej silniki lotnicze. Ten przemysł jest wbrew pozorom bardzo podobny do farmacji, jakość ma pierwszorzędne znaczenie, produkowane silniki nie mogą się zepsuć, tak jak leki muszą spełniać wysokie wymagania jakościowe
- Podejście do UR bardzo się zmieniło. Jak będzie wyglądała praca tych służb za kilkanaście, kilkadziesiąt lat?
Fabryka jest coraz bardziej zautomatyzowana, skomputeryzowana. Wymagania regulacyjne dotyczące np. Track&Trace, czyli serializacji, powodują, że musimy montować na liniach rozbudowane podzespoły służące do identyfikacji jednostkowego opakowania, a co za tym idzie – urządzenia, komputery i systemy informatyczne, które wspierają cały proces. Do tego dochodzi continiuos process verification, który ciągnie za sobą wzrost liczby parametrów które chcemy w sposób ciągły monitorować a co za tym idzie ilość czujników na maszynach. Wszystko to powoduje, że profil utrzymania ruchu zmienia się – obok elektryków i mechaników zatrudniamy mechatroników i automatyków. Moim zdaniem, IT automation będzie za kilka lat głównym elementem wsparcia technicznego. Element mechaniczny pozostanie – zawsze będzie ktoś, kto będzie musiał zająć się np. stemplem od tabletkarki czy popychaczem od kartoniarki.ykonuje działanie poprawnie, to błąd tkwi gdzieś w sposobie zarządzania. Obszar techniczny ściśle współpracuje z technologią i z produkcją. Kiedy mamy problem, siadamy razem i wspólnie staramy się go rozwiązać. Chcemy coraz lepiej rozumieć proces, żeby dobrze identyfikować zmienne na niego wpływające.
Rozmawiała Patrycja Misterek
Fot.: GSK