Wszystko jest trudne, zanim stanie się łatwe
O budowaniu świadomości wśród pracowników, o odwróconej piramidzie zarządzania, o bazie pomysłów, o produkowaniu jakości i o podejściu do zmian mówi Jan Pietras, koordynator WCM w fabryce Fiat Auto Poland.
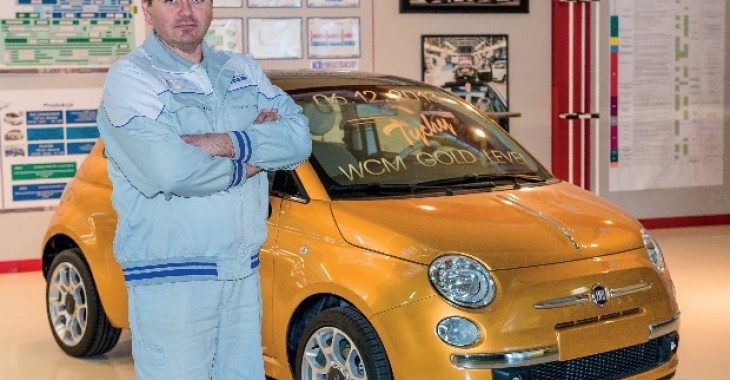
- Japończycy zawsze mieli wiele ciekawych, kreatywnych pomysłów na zarządzanie.
Zgadza się. Przykładem może być podejście według 5S. W latach osiemdziesiątych Japończycy zarządzali w zakładach wykorzystując zasady tego systemu. 5S poprawia jakość, bezpieczeństwo i wydajność, porządkuje procesy i sposób myślenia, ale tylko ogólnie. Na detalach skupia się natomiast World Class Manufacturing (WCM), składający się z 23 filarów: 10 menadżerskich oraz 13 technicznych. Każdy z filarów technicznych funkcjonuje i realizuje swoje cele w procesach według 7 kroków.
WCM jest modelem zarządzania, którego celem jest „zero” strat i „zero” marnotrawstwa. Ten cel jest realizowany poprzez wspólną pracę filarów technicznych. Oczywiście, rozwój WCM w zakładzie zależy od każdego pracownika na każdym poziomie zarządzania. Zasady 5S są bazą do rozpoczęcia wdrażania filarów autonomicznych: Autonomicznego Utrzymania Maszyn, Organizacji Miejsca Pracy, Profesjonalnego Zarządzania Maszynami oraz Logistyki. Jeśli 5S nie zostało wdrożone w zakładzie, to nie ma sensu rozpoczynać pierwszych kroków dla filarów autonomicznych – dużo się napracujemy i niewiele uzyskamy oszczędności.
- Najpierw ogóły, potem szczegóły?
Na początku trzeba zrozumieć, na czym polega problem i jakie jest zjawisko powstawania problemu. Nie da się zagotować całego oceanu, ale jeden litr wody zaczerpniętej z niego tak. Chcemy dotrzeć do szczegółów i pojąć, jak działają. To jest właśnie ten „jeden litr wody”, którym zawsze możemy zarządzać. Oczywiście, to podejście wymaga od pracowników wiedzy, umiejętności i odpowiedzialności na każdym poziomie w piramidzie zarządzania zakładem, zaczynając od dyrektora poprzez kierowników, team liderów i kończąc na pracowniku liniowym. Od ogółu do szczegółu, ażeby połączyć wymagania naszych klientów z procesami, które je tworzą.
- Na pewno bardzo ważną rolę odgrywa tu świadomość pracowników.
Według mnie świadomość podejmowania zmian dla ciągłego doskonalenia jest najistotniejsza. Nie spotkałem jeszcze osoby, która nie chciałaby robić czegoś lepiej (choć każdy wyjątek potwierdza regułę). Jednakże same chęci nie wystarczają. Tworzymy know-how. Uczymy pracowników metod postępowania po to, żeby wiedzieli, jak przekształcić swoje pomysły w realne czynności, które doskonalą nasze procesy.
- W tej chwili macie poziom złota – 73 punkty. Zbliżacie się jednak do poziomu 85 punktów. Jest to już zarządzanie przez duże „Z”…
…ale paradoksalnie wszystko zaczyna się od „dołu”. Piramida zarządzania jest odwrócona. Każdy pracownik w procesie produkcji ma być menadżerem w swoim obszarze pracy. To pracownicy tworzą wartość dodaną dla klientów i jest bardzo istotne, żeby podejmowane przez nich decyzje były właściwe. Oczywiście, otrzymują oni bezpośrednią pomoc od swoich team liderów, którzy zarządzają grupą od 6 do 10 pracowników i biorą za nich odpowiedzialność.
- A jak szkolicie pracowników?
Celem WCM jest „zero” strat, a jeśli się kogoś uczy i nie jest to potrzebne, to powstaje strata. Zgodnie z podejściem filaru Cost Deployment, analizujemy wszelkie marnotrawstwa. Wiemy, gdzie strata powstaje. Jeśli
przyczyną źródłową „błędu ludzkiego” jest brak wiedzy pracownika lub niezrozumienie, jak powinien dobrze wykonać czynność, wówczas wykonujemy ponowne szkolenie. Upewniamy się, że pracownik zrozumiał i że wykonuje czynność zgodnie z ustalonym standardem pracy. Poprzez szkolenia zwiększa się kreatywność pracowników. Od wielu lat realizują oni swoje pomysły zgodnie z metodyką „Quick Kaizen”.
- Ponoć według filozofii Kaizen nie ma głupiego pomysłu.
Pomysł jest najgorszy wtedy, kiedy jest tylko jeden. Są pomysły, które z różnych przyczyn nie mogą być zastosowane. Później takie, które od razu możemy wdrożyć i dają nam realne oszczędności. Wreszcie są
i takie, które będzie można wprowadzić w życie, ale dopiero za jakiś czas. Pracownicy przekazują pomysły team liderowi, on zapisuje je w systemie, a następnie są one analizowane przez zespół złożony z przedstawicieli filarów Focus Improvement oraz People Development. W ten sposób powstaje baza pomysłów. Pomysły naszych pracowników przynoszą zakładowi w każdym roku znaczące oszczędności. W zeszłym roku w naszej fabryce powstało kilkadziesiąt tysięcy pomysłów. Najlepsze z nich są nagradzane, zgodnie z systemem motywacyjnym.
- Wspomniał Pan wcześniej o odwróconej piramidzie zarządzania. Istnieje pogląd, że stanowi ona kość niezgody. Głównym filarem firmy są bowiem operatorzy, bo pracują w miejscu, gdzie powstaje faktyczna wartość. Dyrektor czuje się wówczas mniej dyrektorem, ma poczucie, że jest mniej ważny. Co Pan o tym sądzi?
Uważam, że dyrektor powinien czuć się dyrektorem przede wszystkim wtedy, kiedy jest w Gemba. Nasz dyrektor
tak właśnie do tego podchodzi. Oczywiście ma swoje biuro i musi być tam dostępny, ale w określonym zakresie. Na co dzień wszyscy jesteśmy tak samo ubrani, mamy takie same ubrania korporacyjne. Tworzymy jedną grupę, w której wzajemnie się szanujemy bez względu na stanowisko, ale każdy wie, co ma robić, zna swoją funkcję.
- W lean operatorzy są właścicielami procesów i maszyn. Czy u was też tak jest?
Tak. Celem filaru Autonomous Maintenance jest utrzymanie warunków początkowych maszyn oraz środowiska pracy, które zostało stworzone. Kiedy kupujemy sprzęt do domu, to również chcielibyśmy, żeby przez następne 10 lat był on taki sam i działał tak samo dobrze, jak w momencie nabycia. Operatorzy pracują na liniach produkcyjnych przez 8 godzin codziennie i „opiekują” się swoimi maszynami. Znają je jak własną kieszeń, znają każdy zawór, mechanizm.
- Czy autonomiczne utrzymywanie maszyn wpłynęło na zmniejszenie liczby awarii?
Kiedyś, jeżeli coś złego działo się w maszynie, to pracownicy UR reagowali po dłuższym czasie ze względu na obszar zakładu i znaczącą liczbę maszyn. A z małego przecieku robiło się tsunami. Operator jest na miejscu
i ma świadomość, że to on jest odpowiedzialny za swoje stanowisko pracy. Jeśli widzi jakiekolwiek zagrożenie,
niedoskonałość, niezgodność daje informację w postaci karteczki w odpowiednim kolorze, która umożliwia odpowiednią reakcję służb UR. Dzisiaj, sami operatorzy potrafią wykonać czynności, które zapobiegają awariom. Przynosi to wymierne oszczędności finansowe.
- Nawiązując do finansów, czy okres kryzysu, z jakim miało do czynienia większość branż w ostatnich latach, dał wam się we znaki?
Może niektórych zaskoczę, jeśli powiem, że WCM pozwala uzyskać najwięcej mocy i energii właśnie w czasach
kryzysu. A kiedy kryzys się skończy, będziemy mieli „właściwą prędkość”, żeby wspiąć się wyżej. My cały czas
przyspieszamy i cały czas budujemy know-how. W tej chwili czekamy na nowe wyzwania, na które jesteśmy gotowi. Pracownicy są przygotowani, żeby produkować najwyższą jakość dla klienta, bezpiecznie, wydajnie i jak najtaniej.
- Gdzie jest ta granica pomiędzy niską ceną i wysoką jakością?
To klient decyduje, jaki chce kupić wyrób i ile może za niego zapłacić przy danym wyposażeniu. Pewnie zawsze będzie taka grupa ludzi, którzy będą kupowali najlepsze samochody bez względu na ich cenę, ale jest to niewielka część społeczeństwa. Trzeba więc dopasować produkt do klienta, przekładając jego głos na swój proces.
- Czyli Pana celem jest całkowity brak braków?
Tak, moim celem jest zero awarii, zero mikropostojów, zero braków jakościowych. Do takiego stanu w naszych procesach podążamy. Każdy z nas jest klientem. Codziennie coś kupujemy. Czy ktoś z nas chciałby kupić samochód, gdyby wiedział, że ma usterki? Chyba nie muszę odpowiadać.
- Jak więc osiągnąć magiczne „zero”? Czy jest to w ogóle możliwe?
Odpowiedzią jest WCM, który daje narzędzia i sposoby postępowania, pozwalające zakorzeniać w ludziach „świadomość zera”. Poszukujemy przyczyn źródłowych strat, wykorzystując nasze know-how. Pracujemy w sposób systematyczny i zgodnie z ustalonymi standardami. Takie podejście zawsze pozwala osiągnąć „zero”.
- A gdyby przenieść Pana do zupełnie innego zakładu, np. farmaceutycznego, czy tak samo szybko się Pan odnajdzie?
Specyfika produkcji nie ma tutaj żadnego znaczenia. W każdym przypadku pracownik nie powinien popełnić błędu, robot czy maszyna wytwarzająca wyrób ma się nie psuć i ma produkować jakość, żeby klient był zadowolony z samochodu, a pacjent poczuł się lepiej po zażyciu lekarstwa. To właśnie jakość. Można ją różnie mierzyć, ale podejście jest takie samo, zmieniają się wyłącznie parametry procesu.
- Czy zdarza się Panu usłyszeć: „my jesteśmy małą firmą, nam nie opłaca się bawić w WCM”?
Jasne i to często. Pytam wtedy: „ale co się wam nie opłaca?”, i w tym momencie pojawiają się trudności z uzasadnieniem tego poglądu. Problem tkwi w nas, bo większość ludzi po prostu nie lubi zmian. Uważamy, że jeżeli robiliśmy coś dobrze przez 20 lat, to czemu to modyfikować czy ulepszać? Sprawdza się tutaj metoda małych kroków, rozpoczynając od stanowisk modelowych, które następnie rozszerza się na kolejne obszary zakładu, powoli i systematycznie. Trzeba pamiętać, że wszystko jest trudne, zanim stanie się łatwe.
Fot. Fiat Auto Poland Sp. z o.o.